- Home
- Collections
- HONNOR DH
- Honnor Well Drillers Ltd Business Summary 1953-2003
Honnor Well Drillers Ltd Business Summary 1953-2003
1953 — 2003.
50+ YEARS IN WATER ASSOCIATED BUSINESS.
Doug Honnor, 4th. Oct. 2003.
PRELUDE: PLUMBING – PLUMBER
The latter word plumber is derived from a Latin word plumbum meaning “lead worker” The Roman lead artificers were (among other arts) dedicated to production of lead “cisterns” to hold water for drinking. Utensils for dispensing water inside and make flashings to keep rainwater outside buildings. They were skilled in constructing gravity supplies (ducts) & had even developed early forms of the piped systems we are familiar with today.
Water :— This is such a unique compound of H2O we all take so much for granted, particularly in our country of plenty. While it can be made to and have many physical changes, it cannot be destroyed (thank God). Throw it on red hot surface and it will flash off into the atmosphere. It is the only substance I know of that expands when frozen (ice, just as well). When passing from liquid form, it can be a gas (steam), a vapour (both invisible) and condensed visible dew (cloud, fog, mist). While snow and hail being fascinating, but are just another form of frozen. What other substances are indestructible or without permanent chemical change? Laboratories have endeavoured to separate water’s two elements which would make an ideal combustible fuel. But maybe to the good, that the cost of achieving this outweighs any benefit, — so far. Another wonder is the enormous amount of water the atmosphere can absorb. Just think of a thunderstorm where an inch (25mm) of rain can be released in a matter of say 2 hours – or less ! Now 1 inch over an acre weighs 101 tons, = 22,650 imperial gallons. Hard to imagine those millions of tons deposited in this short space of time just on our local plains. How does the atmosphere hold, then release such horrendous weight ? —– Absolutely amazing !
Down through the ages man has always been a slave to this vital resource, Archimedes having designed the first screw-type “pump” and Da Vinci improving on it in the 1500s. Hence plumbing has evolved in recent centuries to what is today a varied and complex highly skilled engineering trade-profession; maintaining the essentials of delivering clean potable water to the populace then piping away wastes and effluent with all the complexities of efficient and safe disposal to guard health of the nation. Other facets of the trade require making buildings waterproof – flashings, (design faults have failed this in some instances in recent times) efficient safe disposal of storm water, hot water installation, heating and ventilating, the latter now known as “mechanical services” Also sheet metal, gas and electric welding abilities in addition to the art of soldering. Some country plumbers have to be good “all round” craftsmen who are able to efficiently tap into springs, supply, install and service all types of pumps to shallow and deep wells. Also care and maintain, well-heads, draw offs from all types of sources. Some plumbers have become involved in water well drilling.
Overall and with such varied facets dedicated around water, can make plumbing an interesting and fascinating skilled occupation where one can sometimes move to different types of jobs, meet all types of people and challenges during course of a weeks work.
(It is unfortunate that some facets of the populace in their gross ignorance just regard plumber as a man who fixes your blocked toilet)
In the winter of 1953, age 24, I set up a plumbing business in Hastings, having previously served apprenticeship and worked from 1944 for 6 years until 1950 with Liley and Horton,
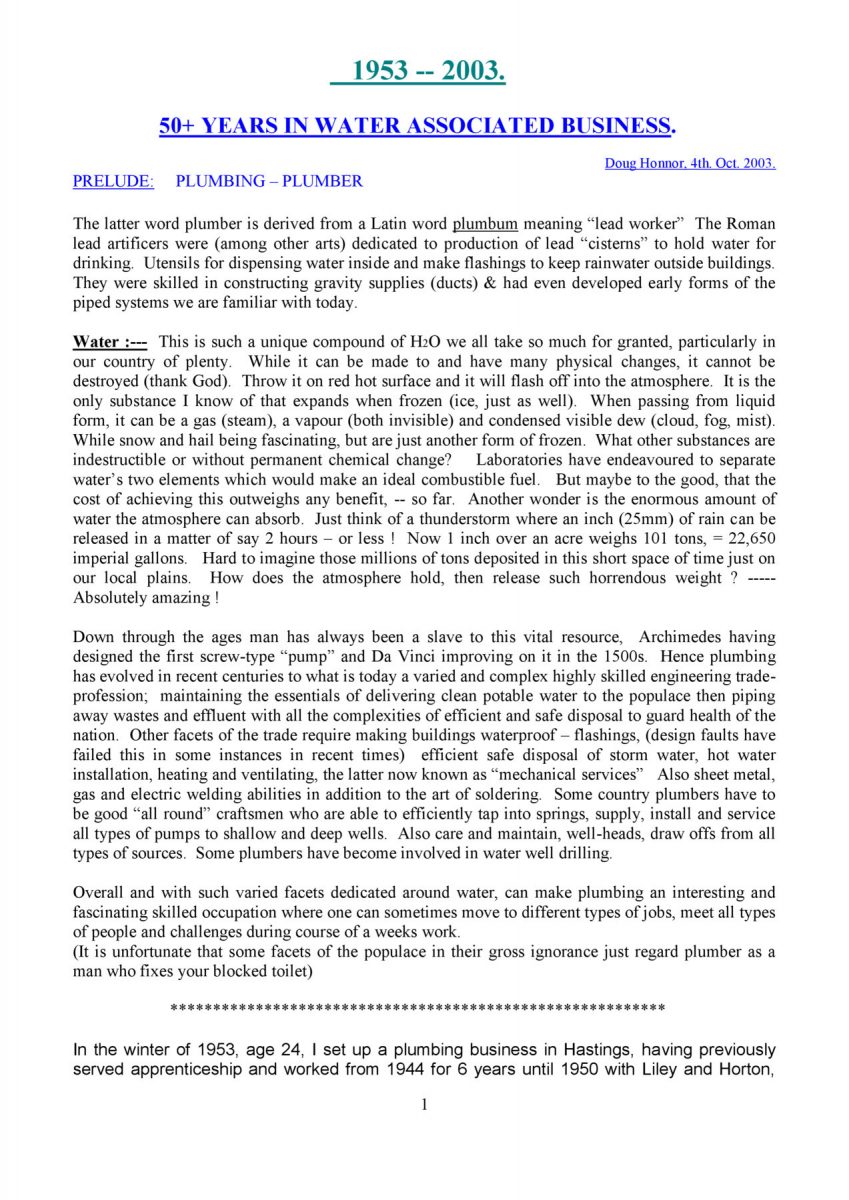
Page 2
(Brian Liley’s and Greg Horton’s fathers) plumbers and sheet-metal workers where plumbers had to be more versatile in the 1940s where in addition to general plumbing we were required to recondition vehicle radiators (don’t know if such “specialists” were about then) also service piston pumps, have sheet metal capabilities and make numerous large galvanised water tanks – all riveted and soldered joints – no “goo” in that era. I recall Herb Jillings and Les Liley (the boss), once had a competition and each made a 400 gallon tank in 4 hours, only helper was the “dolly boy”(me)- exceptional going and don’t think they leaked either! Herb was an excellent & neat tradesman, became a great friend in latter years.
After completing that six years with the old firm, then spending a further 3 year stint working and saving around Australia, was able to commence establishment back in the old home town. Although work was readily available, materials and equipment were sometimes very difficult to obtain. For instance a suitable tradesman’s vehicle was a real major item to obtain; nearly all being pre-war trucks, some even having to make do with later 1920s models; however, most were in the 1930s models with model A Fords quite common. During and after the war, large numbers of cars were converted into light trucks for farm and tradesmen’s use, it being hard to believe today how desperate the shortages of such were. Another incentive to convert cars into trucks was a more liberal petrol allowance where it could be proved justified. Indeed petrol rationing wasn’t finally dropped until 1950! However, me being a cash buyer was fortunate to obtain a relatively “late model” 1936 Chev truck which was also a converted 7-seater car which made an ideal truck for those days but still required some dedicated T.L.C. after paying £250.0.0. (In today’s 2003 money, this equates to paying $12,000 for a 17 year old well used light truck/Ute). A reliable and presentable vehicle being one of the many necessities which is taken so much for granted today (It may seem hard to believe, but there was a Hastings plumber in 1953/4 who operated his business on a push-bike; he got merchants – builders – owners to arrange delivery of materials to the job). Post-war vehicles were about, but very expensive and not readily available.
’36 Chevrolet.
My 1936 plumbing truck, owned 7 years, 1953 – 1960.
gave great service. It was originally a 7 seater car, but during the war shortages it was professionally converted to a light truck as were many then to help the war-effort.
It looked quite smart with pale green body & yellow wheels. – Good mate, Ray Chappie posing.
The next major steps were increasing plant and material stocks after having constructed own workshop at Aunty & Unc’s orchard on the outskirts. Found then it was good practice to order well ahead and in larger quantities where possible as there was only one mediocre plumbing merchant in H.B. then and Napier being only a secondary port, therefore any larger orders were made through main-centre merchants via travellers, with most imported goods coming to H.B. via Wellington port or distribution centres for N.Z. products from Palmerston North, Hamilton or Wellington, so it was in several ways advantageous for those who could, to stock up and carry goods. I purchased earthenware drainpipes from Plimmerton factory
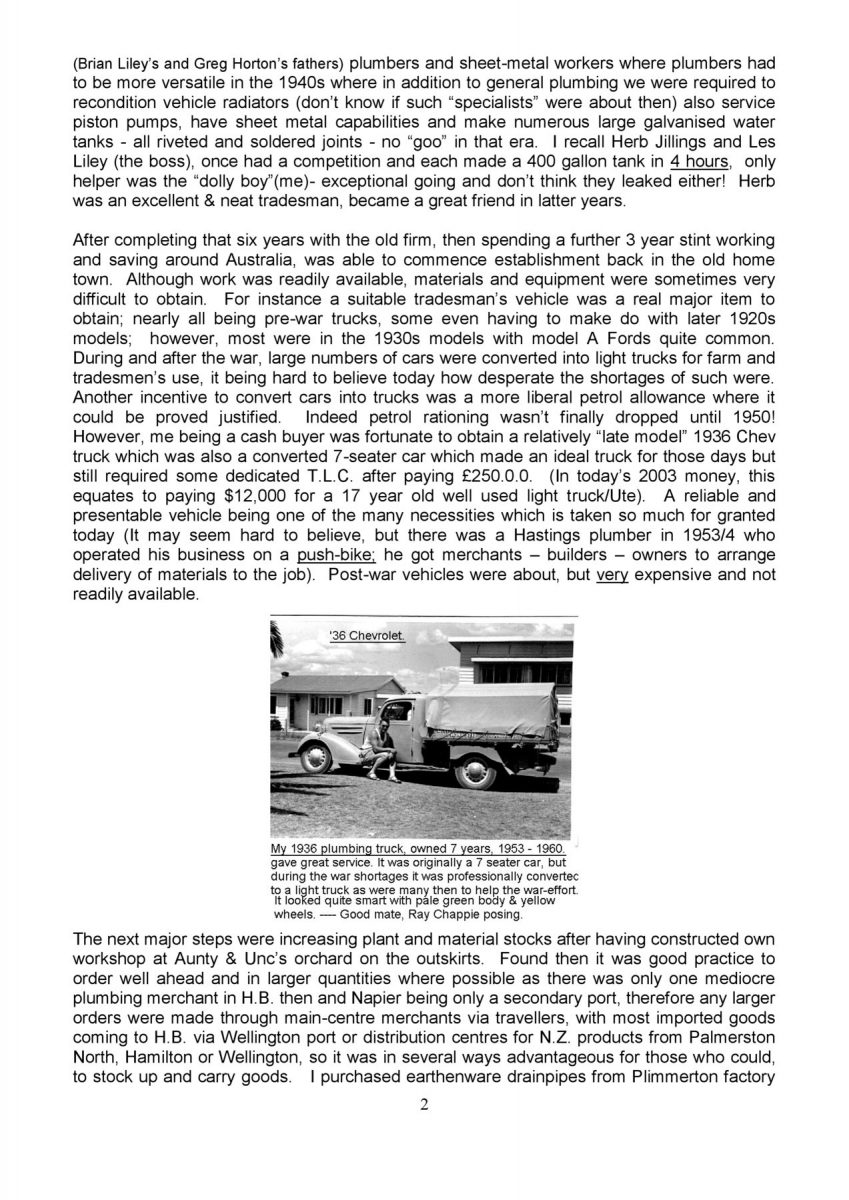
Page 3
by a railway wagon-load which in the long term paid handsomely as well as alleviating shortage of the odd vital fitting. Indents of galvanised fittings could be compiled about 3 months in advance which arrived in barrels from England, although not necessary (Taiwan unheard of), but well worth-while price-wise. A far cry from many operators today who work out of a van and buy hand-to-mouth. Materials were much heavier in the 1950s – earthenware drain pipes, cast iron baths, much iron pipe (some copper), no plastic tanks; P.V.C. was unheard of and polythene pipe was trying to be introduced in early 1950s with many sceptics. Therefore a truck rather than a van was the essential order of the day.
After firstly making do with a large table for office work, another necessary early purchase was a fine Rimu desk which I engaged good friend Don Burgess to make to specification. It could be said the business was founded and directed from this desk for the next 40 years and still exists today, good order, in back room semi retirement.
So having accumulated many of the basic essentials, the other major outlay at the time, being first, was a brand new sheet-metal folder 1953 /4; to do one most proud. Having thought about such outlay for making essential flashings etc but standing idle for much of the time, set about finding what other purposeful use it could be put to. Now it so happened there was a demand for lead-edged ridging in Hastings, for at the time the major builder’s supplies were receiving it spasmodically from Palmerston North often with the lead badly damaged on rail transit. So set about making attachments for the folding machine to form and make ridging, other attachments to make spouting, barge-cap and roll also a beading machine from basic components. The several first runs of ridging were cut by hand by helpers & self with 12” tin snips. 140 sheets for ton at a time, — unbelievable now! So urgency to await arrival of a new “Burts” guillotine (another item not readily available) which was a godsend in 1954. Stress there was no long-run or crimped ridging, spouting (guttering) etc then, everything in 8ft (2.4M) lengths. The iron used was 30” width ordered in 1 ton lots, so one cut made two 15” (380mm) strips for ridging. The machine was set up so one man could form the strips into ridging. The best time I made was 1 ton in 3 ½ hours equated to 2,240ft (683M). Now the most time consuming part to follow, was soldering the lead strip onto each blade of the ridging where part time semi-skilled workers assisted on contract. Having kept annual production log, the best year, 1955/6 produced 6 miles of ridging meaning 12 miles of lead strip was soldered onto using large “hatchet” irons, a good man could do 24 strips (12 lengths per hr). Lead strip was purchased in ¼ ton crates and solder by the 1 cwt (51 kg). In addition to the ridging, much barge cap, roll, copper and galvanised spouting was manufactured to order. So outlay on machines turned out to be admirably justified with “good profitable return on investment”.
Other general workshop equipment was accumulated, rollers, beading machines etc to ensure efficient operation as many items were made rather than purchased, i.e. fluming, chimney cowls, some instances – case, lag and convert cylinders. Make large water tanks and many small 30gal supply tanks – no plastic tanks then. Such workshop operations were mainly reserved for wet day, nights and/or fill-in work (other than urgent) so one was always kept fully occupied and helpers didn’t have to “stand around”. These workshop “sidelines” were of great assistance in consolidating the business. Was extremely busy (but this fit single man made time to play hard too after long working hours)
General Plumbing
This was the main operation & with good friend Ron Edgar’s help; one of the early jobs of significance was involvement in major refurbishment of the old Havelock North (McDuff’s) Hotel, since demolished and now the Happy Tavern.
(*Ron, a hard working skilled man from a humble home who also started from “scratch”,
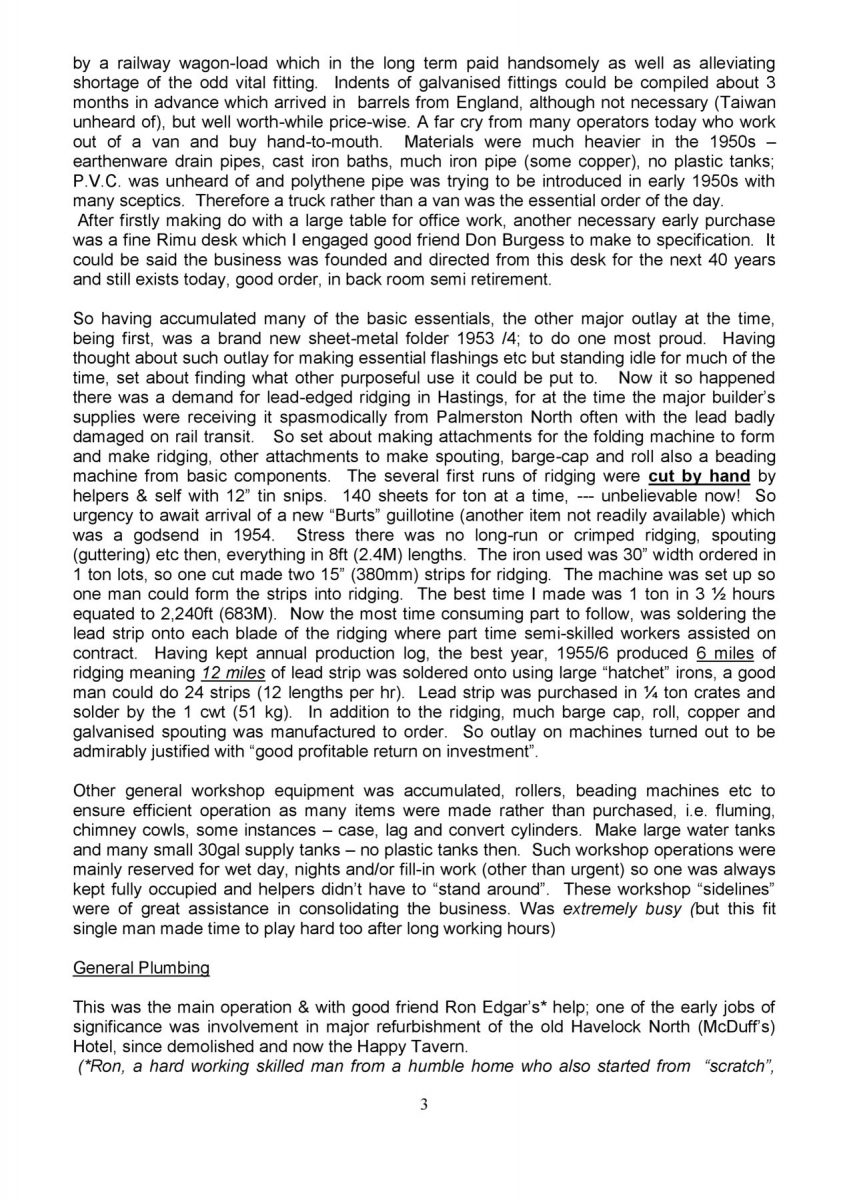
Page 4
subsequently founded a highly successful plumbing business in Browns Bay, Auckland)
Materials became more readily available and better variety from mid 1950s onwards, apart from motor vehicles. Overseas funds were required to import certain commodities. Other plumbing consisted of several large new country houses, Kereru Station new and maintenance, new urban houses, some new commercial which would total about 1/3 of time. The remaining 2/3 on alterations, renovations, repairs, maintenance, pumps, water supply and farm reticulation. Being involved with many orcharding and horticultural clients: modifying their well head works and setting up early basic irrigation and pumping systems.
Also in the 50s and onwards, there was much demand for large, quality farm homesteads, being on hold during the war years, then with the many returned soldiers settling on Re-hab. farms combined with the massive wool boom, farmers in general had much money to spend on overdue improvements such as fencing, sheep yards, wool sheds, hay barns, reservoirs, improved water supply and numerous other essentials, plus of course good housing to replace some which were little more than antiquated shacks. All of this required skilled tradesmen. Then in addition, there were the older established well-to-do, such as the Central H.B. owners wanting new or upgraded elaborate housing for themselves and their Sons which were settling on the land. So this was the scene of my many new-house country plumbing contracts, some of which, such as Wakarara were considerable distance from Hastings over very rough slow roads to the site access. So it was often common to load up the truck chocka, stay away for most of the week, long days, long hours, where other trades and self were accommodated in quarters with all meals supplied by owners or a cook-house. Much of my plumbing work was contracted to good honest builder and friend, Colin Gordon. I carried out many large home-stead plumbing, drainage and farm water installations for Colin where our association lasted over many enjoyable years. Colin had a very dry round-about sense of humour and there were many interesting experiences and tales to tell, some humourous and some a little odd. I recall one in particular for a new house being almost finished for wealthy CHB farming family. The Son, R.J. and his bride to be, were getting ready to occupy it straight after the honeymoon. One Monday, I arrived back on the job to complete the finishing work and after a while Colin started to tell me a story in his usual roundabout way. Saying matters are not too good and not too sure how the job was going to turn out. Now this got me really wondering about whether owner’s finances had collapsed, or they were dis-satisfied about the job overall, but at that stage there was doubt whether work on the house would continue? Now the story eventually unfolded as follows :— The groom, a nice steady responsible man about late twenties was engaged to a city girl, (Wellington I think) All details were arranged for a large wedding which was to take place within days. Invitations sent, replies received, all the trimmings, catering, dresses & flowers as one could imagine. —And a brand-new home almost complete. The groom cancelled the wedding !! What happened was the bride’s mother implored on her daughter to make sure house was carpeted before they moved in, with words to effect “she knew what these farmers were like and if not done prior, may never get carpets” Now this was about 1954/5 and it was quite common then to occupy a new home before carpeting, for as previously stated many goods were not readily available, therefore often better to wait for superior quality. The groom took this as a personal insult to both him & his family, so after much stress and soul-searching, considered that if these unreasonable demands were made prior, what was likely to be in store for him after the wedding ? So it was cancelled.
I was living in the main homestead with the family during course of the job, therefore subsequently also felt for them having to live through the stress and trauma this hard decision placed on them. The family were united in their support and understanding for this sad non-groom.
There was no delay work-wise, we were instructed to complete the house which really was
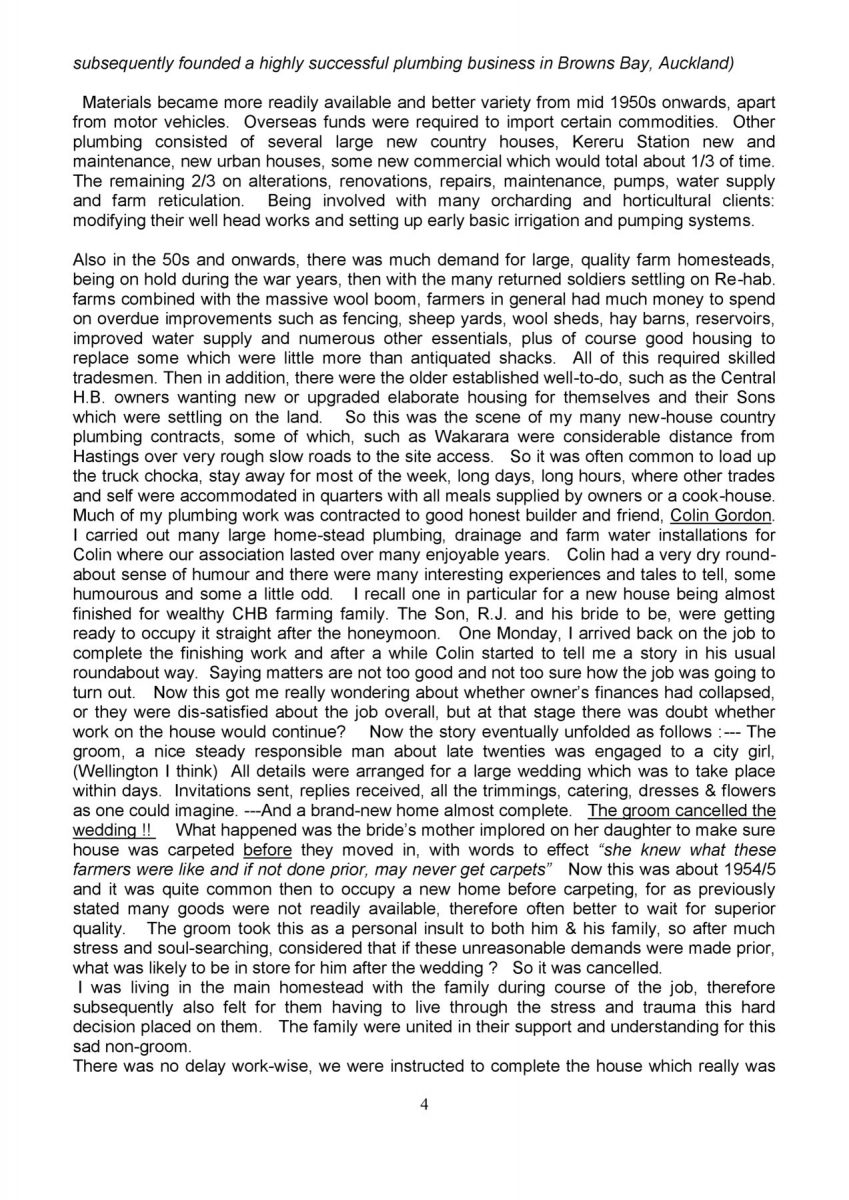
Page 5
the obvious conclusion, — all tidy and paid up. R.J., quite some time later married a local farming girl, had a family and like his father became a prominent public figure. Have often wondered about those bloody carpets, but knowing these people, I bet eventually they were beauts. —– End of story, being just one of the many experiences, although fortunately non [none] other quite like that one. But some customers had funny ideas, such as one insisting new toilet pan be set about 3” lower in its concrete base, so it was low enough for little 3 year old Jimmy to pee in. They didn’t consider a box to stand on and the little fellow had a habit of growing and would ultimately be plagued with a semi-Arab bidet’ forever-after! Then another customer requested a urinal in his new house. He had one doted-on young Son who the builders labelled “King Farouk”. There were no more males to follow, so again wondered what they and subsequent owners did with that expensive peeing-place?
Now being single and with no family ties or obligations during initial three+ years, was able to concentrate profits back into the business. Policy from day one was to always pay accounts on or before time to maintain the 3rd generation Honnor reputation in Hastings. The confidence built up with merchants together with buying advantages in larger quantities (one ton rather than a few sheets at a time) created a more profitable turnover of materials for what was little more than a one man business. Whereas some of the larger businesses but slow payers could in some instances be paying more for their goods. 3½ years after commencing business, I married Doris (December, 1956). My good wife became interested in learning all aspects of small business book-keeping, general office management and its complexities – wages etc. Doris was a skilled ex Post Office Senior shorthand-typist. The only problem was – didn’t own a typewriter! All accounts continued to be sent out in longhand which was relatively common and acceptable in those days. Even many of the larger businesses also used carbon copy hand-written invoice/statements.
Apart from residential mortgage and occasional temporary O.D., the business never used higher interest term loan borrowing under my management, didn’t spend on non-essentials where there were other priorities. The first typewriter was second hand, purchased in 1964 for £30 – wasn’t Doris’s birthday either! In 2003 this would equate to $1,200.00
In the early 1950s many domestic cold water services were done in galv. iron pipe, hot in copper, some were still using iron for waste pipes, there was even the odd lead trap being used with wiped joint (replacements). Most traps and wastes were by then in copper. Sheet lead was beaten and used extensively particularly on tiled roof chimney flashings. There were no plastic traps or other wares until well into the 1960s.
The business had an excellent set of marine plywood collapsible septic tank shutters/moulds where concrete tanks were efficiently poured on many rural sites until into the 1970s. With correct management, this was also a profitable facet. After then, workers became “gun-shy” of concrete mixers and shovels (shovel-shy) where the more expensive (but easier) pre-cast tanks became the order of the day.
During the late 1950s and early 1960s the business was offered and if interested to carry out another facet. On studying manuals, dangerous goods requirement and specifications, courtesy & help of friend Malcolm Gilchrist’s knowledge, found it worthwhile to become involved in oil Co. underground petrol tank, pump and pipe work installations mainly for smaller service stations & commercial users and not impeding on general plumbing maintenance work, found petrol pumps far more profitable at that stage than seeking new house plumbing which at times was being “bought”. So it proved there was financial safety in diversification within the trade.
Page 6
The large steel tanks had to be tested on site immediately prior to being placed in excavation. This was done by air pressurising them to 5 psi, so the dangerous goods inspector could monitor the lather over all seams and pipe joints for slightest trace of tell-tale leak. There were strict specs to adhere to; the tank had to be encased in clean pea metal within the excavation, then immediately have road tanker on hand to fill & weight it down.
Pipe work entailing suction, vent & sometimes remote fill installed, all using double elbows to forgive any settlement. Then concrete beam pattern to support 6” segmented slabs which incorporate Toby boxes for fill & dip access. The concrete work had to be finished with least delay, because in event of seepage or heavy rain flooding the excavation, even a full tank would float to the surface, petrol being only ¾ weight of water. Once the beams & slabs are in place, risk is eliminated. Parts of Napier had stricter requirements due to tidal influence; therefore tanks had to be placed in concrete pit. No doubt much of this has changed over the intervening years. However, it was an interesting, challenging & profitable sideline.
In the early 60s, there became ongoing era of much new-house price cutting resulting in shoddy work & short cuts to gain plumbing contracts. There were several occasions where I had submitted what I considered an honest competitive price, and then to find out had lost the contract by a seriously large margin. So I re-analysed all the costings in detail to find competitor had achieved the jobs for retail price of materials only! In other words, sometimes supplying labour for nothing just to gain the work. Although materials on a new house constitute about ¾ of the cost, the mark up on such does not by any means cover all the labour content. So to offset, some of the tricks which they got away with at the time to name just a few, were: – shortened sub standard effluent drains using left-over builders mix instead of proper fill; no stop valves inside boundary; no crox unions on cylinders; specially obtained underweight sheet lead for roof flashings & caps; skim-soldering spouting joints; at times hiring cheaper semi-skilled labourers instead of tradesmen; 26g. iron where heavier 24g. was specified & so on.
The main offenders in this fiasco were Mr O. & Mr. B. who were endeavouring to take low cost housing work off each other & anyone else they could. So I certainly did not want to get involved in that lot. In spite of this, I still acquired much new house work, most of it better quality & for rural community. The mainstay still remained extensive renovation & repair work, being a source of more steady reliable income, new work being less than a quarter of total. It is ironic that Mr. B’s successor who carried on the business eventually folded. A Napier plumber (Whittlestone) tried to emulate Mr. O & went broke in a big way: — so much for “buying work.” On some commercial jobs Mr. O. made his profit on the extras/variations. Understand for instance Aerial Mapping extras were near or exceeded the original contract! Shrewd moves & perhaps “luck of the Irish” There were many other amazing stories, such as duplicated materials left behind on Mr. O’s jobs that were eventually pilfered & yet he still survived. One example in particular was construction of a large block of motels in Railway Rd. where initial plumbing was done and completed by Mr. O’s outfit. Then about a year later prices were called for a second stage. Mr. O. didn’t get the contract which was awarded to Morrie H. Now an amusing story Morrie himself told me, that when he went down the large site to set out the job, he found laying in the rough grass, completely overgrown, a big bundle of copper pipe and other bits and pieces. These had been left behind and forgotten from the previous stage, (maybe Mr. O. thought had the next stage in the bag) Now this was a windfall for Morrie, almost enough to pipe out the second stage. Understandably and justifiably Morrie didn’t enlighten Jim and regarded it a perk as an offset for all the dirty tricks.
So it was with the above frustrating climate in the industry, some such as the Smith Bros.
Page 7
were not prepared to remain in such an environment in spite of being qualified honest craftsmen. Furthermore, being thrifty Scotsmen, justifiably could not tolerate debtors delaying payments. Although my small plumbing business was sound & profitable, I also wanted to look to further diversification which ultimately brought about entry into well drilling. This became a more rewarding & profitable arm of the business, also with less material items required & much less bookwork for turnover. So in some respects, I have to thank Windy- Mr. O. & Mr. B. for unwittingly doing me a good turn by spurring my entry into well drilling, with the business subsequently expanding into a most successful operation. So the story unfolds as follows: —-
As mentioned previously, having been involved with rural water, pumps and small irrigation systems aroused an interest in a 1964 Taranaki advertisement relating to sale of water-well drilling rigs. So after response and various inquiries a trip was made to Waverley to view situation and Neville Clancy’s operations of his plumbing, drilling, pump and water supply in Waverly district. There were many shallow dug wells in the area (as there were around Takapau – Tikokino in H.B.) Now as with the H.B. pits, these would tend to fail when most needed in summer months, so the Waverley plumbers-pump fitters would clean out bottoms of shallow wells (about 20+ft – 6M) to extend suction foot valve. Often this was not good enough so a hand post-hole auger was engaged in desperation to extend further. Sometimes pump itself had to be placed part way down the pit. This was a somewhat hazardous and in many cases an unsatisfactory operation. In frustration Clancy considered there had to be a better way so dispensed with the post hole borer, refused to have his men go down a dug well ever again by purchasing his first drilling rig, drilling many successful deeper sand screen and other wells. As time went by he had accumulated much surplus equipment and in 1963/4 advertised some rigs for sale. – This is where D.H.H. came in. So after returning from appraisals in Waverley and carrying out what is now called a “feasibility study”, placed tendered offer of £710.0.0 for a small rotary and percussion rig ancillary equipment and minimal necessary items. (This being only a start of much more ongoing expenses). The offer also included requirement for up to 2 weeks on field familiarisation and tuition prior to delivery. In due course the tender was accepted so back to Waverley in April 1964. After a short period gaining further knowledge and experience with Clancy’s team, the Ford No.1 Rig arrived in Hastings late April 1964. There was much plumbing work to catch up with as well as initial work on the rig. The first job in H.B. was to drill out a well which was choked with junk. Shortly after drilled the first artesian well – a 3” in St. Georges Road, having assistance and support from Dave Andrews who had previous drilling experience with Vic Boag, also George Willan who had been around rigs on and off for some years. George is an engineer and his father Tom Willan was a prominent driller in and around Hastings for many years before, during and just after the war.
Page 8
Before my time!
Tom Willan during the great depression, sinking a 3” well in early ‘30s at Hastings Mother’s Rest. Note ancient gear with old truck, wooden mast & manilla rope.
Also note the felt hats.
The building still exists today in Civic Square.
A YOUNG DOUG IN 1964, TAKEN ON ONE OF THE EARLY EXPLORATION JOBS AT POUKAWA. NOTE HARD HATS WEREN’T IN FASHION THEN – OR EAR MUFFS!
It became an extremely busy and demanding time with one having to cope with plumbing work, upgrading the rig, learning as much as possible in this new field and in addition major renovations to our old Stortford St. house, very long-hour days and many 7 days a week.
Now in late 1964, was most fortunate to gain the services of Eric Smith, a most able, hard working very qualified plumber with a hilarious sense of humour. Eric had not long moved from his business in Porangahau to be back in Hastings for his children’s secondary education, was highly interested in well-drilling and found this an interesting and challenging change as he also had a yen for “water-divining “ and was well known in the district being an ex-Napier boy. We got on exceptionally well and enjoyed each others company. Eric being an exuberant story teller. Although I haven’t much faith in divining, there were many people out there especially in marginal areas, who wanted their sites “divined” so Eric was only too pleased to oblige in genuine faith, an honest and dedicated man. Eric’s contacts brought in several water well jobs in fringe areas such as Poukawa, back of Havelock North, Raukawa, etc. Other work obtained in that earlier period were jobs in doubtful areas in which other local drillers weren’t interested, so at that stage was only too willing to fill the gap. Most of these were successful, having always used a deep-well pump for testing & proving in such
Page 9
areas to remove any doubt. Submersibles weren’t in vogue & air-lift as used by some wasn’t conclusive enough meaning some potentially productive wells could be–& were abandoned as non-productive!
Then along came a dry summer and with human nature as it is, many land owners had been putting off spending money on that new well which they “may not need this year’ – if rainfall Is average. Then when the dry hit, would want jobs done “yesterday”. This gave the fledgling drilling arm of the business a great boost gaining much confidence with new customers. It must be said that it would not have been possible to have established this drilling business without the “:backstop” of the sound, solvent established plumbing arm with its associated skills together with much hard and dedicated work. Understandably, the existing three established drillers would not be expected to help this fourth newcomer into the fold, so one couldn’t look in that direction for advice or help in the first year or so. Much assistance was obtained from drillers outside the district, in particular John Benton of Hamilton and Jack Penny of Taupo – a most helpful, kind and generous man who is still kept in touch with (now living in Huntly). Also maintained contact with Neville Clancy and made further subsequent purchases from him.
This little old rig tended to be ridiculed by certain quarters of the fraternity, some feed-back in those very early days that “Doug Honnor wouldn’t survive in the drilling business” (at times almost believed them). Must admit there were many difficulties, mostly technical (fortunately none financial) it was certainly not easy. However, balance sheet showed a worth-while return on first two years of purchasing this home-made rig – so suppose that’s what it’s all about as well as having good customer relations.
After that initial period, demand increased and in winter of 1966 a small light rotary machine was required by a dredging Co. to take core-samples in Napier Harbour which was to operate off a barge supplied by the principals. After much preparation, the Ford rig was craned onto a barge, owned by the Harbour Board and loaned to the dredging Company for the test drilling work and fitted with four anchor winches. An old lag from the Whakariri dredge ribbed saying “Don’t put anything valuable on that barge – it sinks occasionally” – no one took much notice of this guy known as “5-minute Fred”. All went O.K. for first day or so, then next morning arrived to see Horror – the barge had sunk with the rig lashed on board! (Photos). A chop had come up during the night and slopped through the “belting” which could appear water-tight, but wasn’t. Fred had the last laugh and wasn’t so silly after all.
The barge had partly settled on the bottom with top of rig mast only just above the water.
Photo captions –
A proud crew in operation. Jul 1966
A not so proud salvage in progress!
NR [NAPIER] HARBOUR JUL. 1966
Page 10
With the partial buoyancy, it was towed/dragged a short distance to alongside the wharf, divers attached slings and rig was craned out relatively undamaged apart from salt water. Most ancillary gear apart from some loose tools was also salvaged. Now by this time and two days having passed, the press and T.V. were well in on the act – newspaper, radio and national T.V. coverage which at that stage caused mixed feelings of embarrassment. Like many things, as the saying goes “It is an ill wind that blows no good”. However, subsequently, the publicity had a beneficial spin-off overall, particularly as drilling eventually continued and work completed. So by this time the new small-town boy was well and truly on the map.
Now the next immediate task once out of the water was to salvage, restore and see if and how quickly machine could be made operational. A truck and engineering firm in Napier, Nattresses, had experience with salvaging sunken light craft, mainly flipped speed boats. Their advice was not to strip engines etc, but get onto them soon as possible after surfacing. The method was to remove all electrics – generators, starters, regulators, distributors, etc, wash then boil in fresh water. After that, dry in low temp oven and reinstall without delay. With engines drained and filled with flushing oil, they were restarted within about 24 hours, gear running to flush and dry out the system. If left standing without prompt attention they would have only been fit for anchors. Another day was spent by a man with steam-cleaner going over rest of rig structure, bodywork etc, so overall there were no serious repercussions and within a few days machine was ready for action again. The next concern was to have a more sea-worthy barge, so while rig was being restored, the dredging Company had large steel flotation pontoons attached to it ready for rig to be craned back on. There were still many days drilling work ahead, some of which couldn’t be worked when a swell occurred as stabilising winches became unmanageable. Short pieces of casing also had to be added or subtracted during coring work to compensate for the tides. Work was eventually completed to satisfaction and paid for. Overall, a most interesting, but at times, traumatic experience. Owe much thanks to Darcey the diver for the efficient and careful manner in which he carried out his work in the murk by safely placing slings with minimal damage. It was also fortunate Doug took precaution of pre-advising insurance company of activity, so practically all costs of immersion were covered by such.
Not long prior to the Harbour drilling, Eric Smith had taken up offer to buy the plumbing business in Napier where he had served his apprenticeship as his old boss wanted to retire, having regarded Eric in high esteem the offer was highly favourable. Eric had a most interesting, fascinating and adventurous career which is another entire story in itself. We kept in touch over the subsequent years; unfortunately this good man didn’t live to see his grandchildren grow up, was taken by stomach cancer in the early 1990s, in his 60s.
So when Eric left our business in 1965/6 it also left quite a large gap, demand for drilling work had increased which drew priority having outlay in plant and equipment which had to be used, so couldn’t simultaneously cope with plumbing work also and with scarcity of additional skilled labour it would have been shameful at that stage to allow this sound equipped, successful plumbing arm to run down. So it was mutually beneficial when Ewan Patterson appeared after some advertising and he successfully took over the plumbing section on a profit sharing partnership basis for the next 6++ years prior to entering into plumbing representative work. A good man, who is still kept in touch with although now living out of the district.
Mahia This holiday resort beach and farming area 116 miles NE of Hastings was rumoured to experience summer water shortages so with one or two possibilities and probabilities, took a gamble and transported our “circus” up there at December 1967 holiday time with loyal
Page 11
wife Doris/Mum, Chev. car and caravan, kids, Ford rig, service truck loaded and with small yacht in tow plus a helper. The view was that if not much response would make a holiday of it anyway for in those days most took annual leave then. Unlike today building trade, engineers etc, would mostly close down for 3 weeks. The arrival created some interest as a dry period was setting in. The first positive inquiry was inland from the relatively easy productive and known sand screen well area. Some attempts had been made there previously without success and was justifiably regarded as a very doubtful zone. However, by rotary drilling deeper through hard papa picked up a fractured artesian aquifer. The locals were astounded –so was I, news spread and there was literally a queue around the rig placing firm orders. Consequently, the “holiday” became mostly work and not much yachting experienced.
The rest is history. As from that day-on Mahia took off to become an annual event–plus. In the 1972 visit alone we drilled 25 wells, farm-holiday houses – local bodies – sub. Div. Etc. lost count now at over 200 in the general area since that 1967 pioneering gamble. Must also pay tribute to the McNabb family of Mahia. Ray McNabb, a professional fisherman became a close friend from where operations were based while in Mahia. An extremely likeable and humorous character who didn’t ask – but told people who visited his fish shed “You need a water well !” Many an enjoyable hour was spent with Ray and Ena back in those days.
Now there was a not so enjoyable event the following year when I had to return to Hastings for more gear leaving the caravan “safely” in Mahia Camp. The next day was 10th April 1968, — the Waihine disaster. It was also massive disaster out on that peninsular too, many houses unroofed, devastation all around including picking up my brand new caravan, tossing it over boundary fence, then across the road & beyond, smashing it into a trail of 1,000 pieces, —- Complete write-off ! A lucky escape, for had I stayed in Mahia, me too possibly also been a write-off as well. Fortunately caravan was insured, but still an overall loss.
Due to the Mahia connection, another valued friendship occurred with the Duley family of Wairoa. George Duley, an accomplished engineer had been carrying out part-time drilling work in the area. Due to back problems wanted to relinquish his gear which was taken over on understanding all work and inquiries were referred onto our business. George, another likeable, honest and humorous man retained keen interest in the drilling field, was a great ambassador in referrals. His Wairoa property was also used for a convenient depot for many years. Consequently, many profitable operations were carried out throughout the district… Further spin-off was obtaining test drilling work “site investigation” for the two local Councils mainly for their increasing new bridges programme also water wells in the extensive Wairoa area including the local pump company. There is much more that could be told relating to hair-raising access to some of the bridge sites, driving over riverbeds, flash floods etc. However, this compact old 4 W.D. machine proved ideal for tight spots but at times still required tractor or winching assistance. Much coring and penetrometer testing was carried out for the engineers at these sites.
Now having acquired Duley’s machine and equipment, the rig being very basic, set about rebuilding this onto an ex army Chev. 4×4, a major job at the time among other things, twin drum winches, convert to P.T.O. transmission, fit large rotary box, extend mast, build new drive train, shafts, controls and countless other details which took over 6 months to complete, much of this being carried out by Barclay Engineering in addition to own input. Although not pretty, this No.2 machine proved most versatile once finally commissioned in 1968, capable of drilling from a 3” artesian well to depth, in addition to 4ft. diam. X 20ft. auger holes (and deeper with extensions). Casing was driven by use of a substantial water-cooled cat-head which handled a ½ ton hammer. Cat-head was also most effective for
Page 12
jarring back-pulling casing in conjunction with winches. Perhaps primitive by today’s standards but when set up properly it really worked well with one that knew what they were doing–and showed very profitable return, which suppose its all about. Some time later a heavy spudding gear was installed. Machine was also used for bridge test drilling in Wairoa and Waipawa counties then later followed up in actual foundation work with drilled cast-in-situ piles from 19” to 42” diameter, placing necessary casing. Sheep population was prolific then; machine could also be kept busy for Graziers drilling 20ft deep offal and carcase disposal holes fitted with concrete cover which was good stand-by work then. Hydatids requirements required burning or burial. At that time also had services of Bruce Whitworth, a keen man, good rig operator and engineer who helped make up and maintain tooling and machinery.
Much water well work was obtained and carried out with customer contacts made in central H.B., thanks to Doug Ashby of Ashby Bros. Waipawa. They had an excellent large business and at that time did nearly all the pump and farm reticulation works throughout Central H…B having many old and established clients. Service had to be prompt and reliable to meet Doug Ashby’s requests/demands and keep faith with their client. Customer was billed direct by us and not via Ashbys; an excellent and enjoyable rapport was built up over many years with this firm being also plumbers and electricians; with a lasting friendship between the two Doug’s. Now must stress at this stage, no commissions or other gratuities were paid or received between our business or any pumping businesses who engaged us. Made it a policy in very early days this was not a good practice at all. The fact that our well created the source of water and gave follow on work for pump installer with ongoing electrical, pipelines and reservoirs which usually far exceeded value of the 4” or 6” well. So arrangement was mutually beneficial to all concerned including the most important one – the client/customer without commissions being involved.
In 1968 after consultation with accountant & good friend, Rex Ingram, it was decided to change business name from “D.H. Honnor, Regd. Plumber and Well Driller” and form the company “Honnor Well Drillers Ltd” as at that stage plumbing partnership with Ewan was running under name of Honnor Plumbers (and latterly another waste disposal enterprise Patterson-Honnor.) Company was formed with Doug and Doris as share holders. Think Rex may also have had a $1 share along with Doris’ $1. Move being all to the good with varied and expanding activities.
During this period the property in Victoria Street was developed for transition from the 1953 workshop in Miller Road (On Aunty and Unc’s orchard). So after 16 years there, in 1969 shifted business operations to the new workshop on the ¼ acre (Which happened to be at time of man’s first landing on the moon). Having previously secured land with old house thereon in 1963, subsequently constructing new workshop in front. This was a good move being in industrial zoning and more under the public eye.
Due to delays in having lathe work done, I set about learning basics of such; studied books etc and purchased the Company’s first lathe and ancillary equipment etc in 1972. Other complimentary machinery soon followed. All of such, now most vital part of operations.
In that era, in addition to wells and other work, there was considerable demand for bridge foundation work in the various counties from southern H.B. to north of Wairoa, also pole houses were popular then. But in latter years bridge design changed where one (or two) very large dia. Piers were specified which was beyond capabilities of Honnor’s gear, so this was left to larger companies like Richardson’s of Palmerston North and beyond. However, still continued with diameters we could cope with, which were still many. For the layman not conversant with the cast-in-situ (C.I.S.) piling method – a brief outline as follows:- An
Page 13
excavation is drilled with large auger or auger-bucket with casing then placed or driven through unstable material to founding, then hole proceeds to specified depth further into solid (usually mudstone, sandstone etc). A reinforcing cage made, then placed, then concrete tremmied into place as it is not allowed to be dropped over a certain distance otherwise aggregates tend to separate. This operation is usually closely supervised by engineer or clerk-of-works ensuring mix is correct, vibrators used and test samples are taken. Casing is sometimes withdrawn depending on specs. Now this sounds relatively simple – but it usually isn’t! Because invariably water is present and sometimes hole cannot always be dewatered so concrete has to be placed under the water by use of tremmie bucket which is lowered inside the cage and trips open at base ensuring concrete does not pass through water.
Drilling and placing of casing is not always easy where water is present as different methods and tooling have to be used similar to drilling and casing large water well and often through gravels and rocks. Then more equipment is required to muck-out and dewater hole clean wherever possible prior to casting. So C.I.S. method can be quite involved at times. Site positions can also present difficulties, river banks and in flowing beds themselves where gear is at risk if left overnight. In spite of care have had machine flooded and also instances of casing, cages, suction pipes etc. washed downstream never to be found. At times due to access it took longer to get machine in and out of a position than to drill and case the actual hole. The operation certainly had its problems and worries at times also usually being in remote areas of the counties. But overall a worthwhile and challenging segment of my activities. Profits made were well earned particularly with varied specially made ancillary gear required such as saw-toothed core barrels to cut through submerged logs or into rocks which may only be used once for a particular diameter specified which can change from job to job, then requiring another set of different sizing.
It was considered and viewed to perhaps obtain larger bored piling gear for this and other purposes. After much deliberation (although company could afford such) it was decided not to proceed. Some of the reasons being return on investment could be marginal, would have to tender for contracts all over North Island, staffing problems remote from base. There was more than adequate work for our existing gear without having to go beyond H.B. so wisely flagged it away to concentrate more on the main operation of water well drilling, site investigation drilling and associated activities ranging from Dannevirke to Gisborne extremes which was plenty far enough at the time.
Funds were instead utilised in 1973 by purchasing next door 1/4 acre with large house (408 Victoria St.) @ $12,700 which was a good move and before galloping inflation took off. Hard to believe now but inflation ran at an approx. peak of 20% in the 1980s. Some interest rates were more, so overall few, if any investors were better off after paying tax on the interest. Investment in this property was also complimentary to the drilling Company for extra yard space and shed constructed with other independent improvements. All land and buildings under separate title.
Another purchase
With residue from P. Paton’s rig and tooling purchased from his business, 1980 ex Takapau which was in extremely run down condition – a rod-percussion rig with twin clapped out spudding-gears, however some of ancillary gear was valuable. The basics of machine originally ex Richardson’s of Palmerston North So it was set about to assemble a third rig, reconstructing with one-only sturdy spudder, untold modifications, 6”x6” pump and adding rotary box. All remounted onto a 381 Bedford diesel using P.T.O. for heavier requirements or 21 H.P. auxiliary Kohler where less H.P. was required, the latter doing most of the hours.
Page 14
Machine had good draw-works, double drum, ex Priestman, bought from good friend John Benton, a Hamilton driller. Also converted one of original winches for sand-reel and retained cat-head therefore rig was capable of cable tool work to moderate H.B. depth requirements of the time.
In 1980, Son Greg had joined the regular company payroll, having first served a fitting and turning apprenticeship with local engineering firm (ROH). Greg showed keen interest in the industry (when not interrupted with rally cars which came within hairs breadth of taking his life). Greg became involved with work in maintaining and upgrading plant and equipment in addition to learning more about the drilling operations throughout the 1980s; with associated difficulties.
It is hard to credit now in 2003, but 20+ years ago, trucks, plant, tooling and equipment were not in such abundant supply and so readily available as today and what there was, was costly and not always suitable. The versatile crane-trucks we are now so familiar with were just not about. The odd Hiab, but not as good for our purpose. So much then had to be modified to suit. Tooling, bits, machinery parts made in workshop proportionately more than today. It was quite an event when in January, 1980 the company purchased its first NEW vehicles! Two Diahatsu [Daihatsu] diesel service trucks. Used Jap imports were still unheard of, they didn’t start to become available until the late 1980s and abundant quality good buying not until mid 1990s. Some earlier used imports involved doubtful dealers which gave them a bad name; however, a different situation now with abundant quality used Jap. vehicles and other associated machinery so vital to our industry, thanks to “Rogernomics” where restrictions commenced to ease and open up after the 1987 budget and after G.S.T. was introduced in 1986. The used vehicle industry had a 50 year “honeymoon” sellers’ market from 1939 to about 1989. Indeed recall that a good 1939 Chev. De Lux would fetch up to £600.0.0 in 1946; approx 25% more than its new pre-war price! Such were the desperate shortages then which took a long time to subside. So one grew up and experienced an era where you had to make do and not waste – What a contrast.
Now the 1980s, there were several further events. Competition was “vicious” at times and trend was beginning for larger diameter Wells. To meet this, the company had to partly change direction and commence tooling for such. So after extensive correspondence and enquiries (no faxes or e-mails then) went to the U.S. with a view to purchasing much ancillary equipment, learning more about such, even perhaps buying a rig! Now prior to departure August, 1984, our dollar was over 70c US. After return, the Government had changed, dollar floated and was down below 49cUS, at one stage it was 42c! So forced to view alternative arrangements such as making do, buying some locally, having some heavy tooling manufactured in N.Z. & making much ourselves.
In 1986 demolished the 100 year old res/flat behind the 406 Victoria Street workshop and had a new 2 storey building constructed in its place, workshop extension, amenities and store rooms with offices and a retained flat upstairs.
Page 15
Upgrades continued through the 80s, I made and fitted new mast to No.2 rig which was then transferred from the Chev 4×4 onto a Bedford 4×4, 330 diesel (later a 400) with extensive mods including $14,000 on hydraulics; a compact versatile & efficient machine (with a competent operator) with its large diameter auger, percussion & rotary capabilities intact.
In September, 1987, Paul Bower, a long serving loyal operator drilled an irrigation well at Farndon which produced a record artesian free flow for a 6” in Hawkes Bay. The free-flow was 84,000 GPH (382 Cu.M hr) showing a 5’9“(1.75M.) jet off top of casing! (see pict, P. 25) The significant factor about this was that only 3M of coarse slotted casing was used combined with open end which proved that in these coarse gravels was a greater yielder than for more expensive wire-wound screen of similar length. Part of technique in obtaining such was (among other things) to drive the last length with the well flowing, improving development as “casing screen” penetrated the aquifer. Stones, some larger than your fist spewed out the drive – tee. As at 2003 this free-flow record yield for a 6” well has not been exceeded in H.B. Something Paul can still be proud of. However, large volumes approaching this are common in such areas using same techniques.
Our Heretaunga Plains are most fortunate to have such abundant supply of high quality potable water, so good that it can be pumped direct into mains of our cities without need for treatment. Not many places in the world have this luxury.
Another factor in the 1980s saw an ongoing decline in attitudes experienced with obtaining reliable rig assistants. A legacy from our non-disciplined, permissive society amongst some of the younger people, further aggravated by hangovers and sometimes drugs- which hasn’t improved since. Greg complained about workers Doug had employed for his offsider. So it was decided for Greg to have a try from then on and select his own – needless to say, it didn’t prove much better either. So, while Greg was interviewing a prospect, Doug would discreetly go out and have a very good look at and around applicant’s vehicle. While some were quite O.K., the odd one was atrociously untidy. Age of the vehicle wasn’t considered, it was admirable to see an old tidy car rather than a later model mobile trash-can. Object of the survey was “That if a prospect didn’t/couldn’t look after their own property, how would ours’ fare??!! Further point is disproportionate amount of people now who have gone through into secondary school and can’t properly fill in a time or job sheet. Not to mention some with primer 4 (year two) spelling.
As turnover, plant and employees increased into the 1990s, difficulties also increased maintaining and keeping track of gear, particularly vital loose tooling, materials and fittings due to carelessness, such not put away, returned to correct rig/truck etc. Sometimes being difficult to avoid in this volatile, mobile type of operation, but also much due to untidiness which costs countless frustrating hours & $$$ lost each year (I loathe untidiness) However, on observation contemporaries in the industry don’t appear to fare any better. Would like to know the formula to overcome this – perhaps better co-operation and examples from top
Photo caption – 406 Victoria St. Operated from this Addr. for 33 years ’til Nov. 2002
Page 16
management? Or go back to an owner-operator !
1990: Much could be written about various characters that passed through the company over the years, some hilarious, others’ antics unbelievable;–This could be another entire story in itself. On reflection, wonder why boss’ “Work related stress” hasn’t also been brought into the equation? So from here on are just the main events in dated order:-
1989-90 No. 3 was taken off Bedford 381 which had become overloaded and Greg was involved in change-over onto Volvo 6 x 4 mount with extensive mods and improvements including Isuzu auxiliary, G.D. pump etc. This smart looking rig proceeded to carry out deep exploration drilling for Gisborne Councils, was also used in finding water around Poverty Bay and some further north during the early 1990s. Also larger diameter wells throughout central and southern H.B. in addition to the local artesian aquifers proved this combination rig and valuable unit with the increasing demand for larger diameter wells with the other two rigs kept utilised in their own useful capacities.
Business continued to carry out much of associated work in increasing amounts with demand for larger submersible pump installations requiring heavier servicing gear, hence the eventual addition of 2 crane trucks for this and handling of increasingly heavier casing, large welders etc. etc. Well grouting, sealing old artisans also continued and larger headwork’s with much engineering, welding and cutting in addition to general maintenance and improvements to equipment was ever expanding into the 1990s.
1993 No.1 Ford rig 4 x 4 had its 3rd make-over as with the right operator and its compactness still had a high earning capacity. In addition to its general mainstream water well drilling up to 4” (& the odd 6’), was ideal for re-development, deep-well pump servicing & testing, site investigation-test drilling. Also particularly versatile where instances of confined access were involved, this machine remained a good profit-return unit. Furthermore, for the most part, was set up where it could be efficiently operated by one man, — a 40% in labour savings!
Photo captions –
No 3 Rig.
Volvo as commissioned Nov. 1989 with original mast (later changed)
A very smart & versatile combination machine with new independant diesel power unit.
Nov. 1993.
Ford No 1 compact Rig ready for action again after 3rd. re-furbish ($10k+)
Ideal for difficult sites & one-man operation.
Page 17
1994 Company installed its first computer, instigated by requirement of H.B. Regional Council to co-ordinate well logging – a good move. Cell phones followed close behind with very mixed blessings as to their time-saving versus time-wasting potential. Then followed extensive R.T.systems. It is amazing; the business was able to efficiently run for 40+ years up to then without these impedances – So much for “progress” of which it has become a necessary everyday part of life to conform to these dubious advances. Indeed, I know of at least one successful business (and there must be many others) which don’t allow outside cell phone contact to their job. All calls are handled by land line to office (as always in the past) then if “super urgent” office will then contact the non-listed site cell-phone or R/T. Makes sense for I have often observed expensive machinery shut down while operator attends to these interruptions. Cost-benefit must be doubtful in situations of so many non-essential calls that could have been dealt with by office or attended to at appropriate time later. Conclude that if managed correctly, cell phones can be a marvellous asset; if not they can be an expensive curse!
In September, 1994, I went into hospital for a long stretch (pancreas). So with our office lady, plus Doris and Greg in charge of management, Greg receiving substantial remuneration in way of further profit sharing, the business continued to cope.
1995 TONGA – Greg’s Project. This being the first off-shore venture with some apprehension. The requirement was for three 10” wells to be constructed for heat exchanging system for a new power station. Design principals being Australian consultants to which we were responsible (assume most of the funds originated from the World Bank or similar). There were many logistics required in shipping not only the No.2 rig in reliable order but all the ancillary gear secured and safe for extended period. Work was carried out to satisfaction, without too many barbs overall. The locals being attracted to thieving the hardwood staging blocks. Understand stolen oxy bottles also could make good church bells, how’s that for hypocrisy!
In reflection, if plenty of work in N.Z. North Island – stay here. The rig wasn’t returned direct, but via the Chatham’s route which caused much salt air damage. Greg went to the trouble to attach strong lifting eyes, but the Napier wharfies slung from underneath instead on unloading, causing minor stress and dislocated the rear springs. Much tidying up was required after return and there was also inconvenience of being without some ancillary gear back here in addition to jobs machine subsequently required for locally during absence. There is much down time in preparing, shipping and restoring which must be built into overall cost of such projects. However, an interesting challenging exercise and experience which still came out with some profit; — just.
1996 Oil/-gas well exploration: Requirement was for a local drilling company to carry out what is known as “pre-collaring” or installing starter conductor casing in preparation for the oil rig to subsequently move in and commence the main deep well. The first of these our company carried out was at Kereru Nov. ‘96 (non productive) and over recent years several more including Geo thermal pre-collaring at Kawerau, Wairoa District, productive (gas), Central H.B. and the closest to Hastings being Mangateretere in the high volume artesian belt which created much additional involvement and care with choking off these high water yielding gravels to base of aquifer. A precarious operation that ultimately required “triple-scoping” just for the pre-collaring work and prior to Indo-Pacific commencing main well proper. Much bentonite and grout was used on this one (unlike previous). Then after main well completed and proved non-productive, our grouting services were again required to meet Council specs.
Page 18
1996-97 Telescopic mast was constructed over this period by Greg to replace that on No.3 Volvo rig. New mast provided better working conditions with its haul-down system, hydraulics and many other associated improvements over and above previous which was not designed for current requirements. The strong old mast has nevertheless been put to good use and now stands as a signage icon today at entrance-way to the Company’s Omahu premises and workings.
March, 1997 After meetings and discussions between ourselves and accountant, it was arranged for Greg to purchase the Company and take control from April, 1997. This would commence to release Doug’s funds and was most favourable to Greg as conservative valuation was struck at July, 1995, being somewhat less than the then current value. Furthermore, arrears payments were spread over ensuing 11½ years. Doug retained minor shareholding and with funds in current account also remains a director. Activities also further curtailed by 60% hearing loss due to years of industrial noise.
May, 1997 It was looming H.B. turn to run the National Drillers’ Conference. Greg and team spent much dedicated prior time & effort in organising this to be held in Napier. There were many displays and booths from N.Z. and overseas. The weather held off sufficient for several outdoor activities including our Volvo with its new telescopic mast on display, also being utilised for safety harness and welding demos etc. The Napier venue was ideal with a novel games feature one night keeping all entertained & a ball on final evening. Subsequent feed-back & letters were complimentary, which was most gratifying relief to recipients as it is always difficult to gauge in advance with the element of success being reliant on so many variables. – Well done!
1998 A windfall in the form of Murray Gillies joining our staff having been long experienced in the industry with larger diameter deep wells throughout the district. Having been dissatisfied with his previous stressful situation and away from it for a short while, after subsequent deliberation and discussions with Greg, agreed to come to us for a while before perhaps starting out independently.
During the course of the year, Murray was more at ease; both he and Greg would like the Company to have another versatile machine. So the three of us had a formal meeting at Murray’s place, as I didn’t want an expensive imported machine to arrive without adequate operators. Murray being keen to see such a machine here pledged to stay on with us if one arrived. So it was agreed – “Go to it”
Greg subsequently went to Ontario and was fortunate to meet the hospitable and genuine Canadian vendors – The Knox Family who had an Ingasol Rand T.H. 60 for sale. During finalising the deal, they were most helpful, also accommodated him in their home. There were many difficulties with transportation, bureaucrats and French speaking, via Quebec through which rig had to be transported to eastern seaboard. Greg could relate this story in much more and better detail. However I had great admiration for the Knox Family in not further holding up departure, for they allowed Greg and rig to leave their yard before a substantial payment was cleared into their bank. I could not transfer amount from this end until deal was finalised and $ known. N.Z. $ was buying 72c Canadian at the time.
The T.H. 60 duly arrived in Auckland on roll-on-roll-off ship in November, 1998 with its 700CFM/300PSI compressor. After all the formalities, it was eventually cleared with much tooling and rods that came with machine. Then more work to conform to N.Z. road transport requirements, on spot financing and payments etc which overall took about 3+ days before
Page 19
cleared. And “Lo and Behold” Greg had a job accepted in Kawerau, so headed there with new machine, carried out work to satisfaction on the way. So machine was already commencing to pay for itself before this No.4 rig arrived at our Hastings base.
Much more tooling and rods were made and acquired for this ideal machine including large air powered hammer. Improvements and accessories for this and other machines were and still are forever ongoing.
Larger diameter and deeper wells with increased demand continued late 90s and into the new millennium further acquisitions included a small 4 x 4 Isuzu ex earth-pin driver, which Greg subsequently extended mast, had fitted with a T.H. drive and mast-mounted winch to become compact No. 5 rig which required independent air supply where needed. Machine is handy for smaller jobs and light auger work etc.
2000 A late model 900CFM, 350PS1 Ingasol compressor with 400 HP Cat diesel was purchased. This high capacity unit, the largest in H.B. being essential accessory for drilling/developing some of the larger irrigation wells, was subsequently mounted onto our 4 x 4 Hino truck for mobile back-up to any rig.
2000-20001 Another off-shore venture took place for undisclosed reasons. This time to the Chatham’s. Again there was much preparation and organising to be done, with some of previous experiences under the belt which helped a little. Several wells were carried out over spasmodic periods spanning approx. 9 months, meaning flying crew over there when another job was required. Some were water wells for crayfish industry etc, also some site investigation work. No.2 Bedford rig was used again (as for Tonga) plus a good Mazda diesel service truck, the latter being placed in a container with all ancillary equipment.
As the time drew near to shipping all back, the Chatham locals had taken keen interest in the 4 x 4 rig mount and also the 3.5 Mazda diesel, so it was arranged to sell them both there. This meant cutting off the rig with much dismantling from the P.T.O. system and leave the Bedford cab and chassis plus the Mazda sold to the locals to just leaving rig module, mast and container to ship back. This was a good move arranged by Greg as in addition to locals gaining two trucks, it saved us shipping costs and better price was achieved than on mainland. Now that’s the good part. The machine and all equipment had been safely shipped to and from the Islands, twice loaded and twice unloaded – quite a business. The equipment was safely placed on a transport firm’s truck at the Napier Port ready for the short distance to Hastings. Now for the bad bit – truck turned a corner in Napier and spewed rig module over the road, hell of a mess with twisted bits, ruptured hydraulic tank with oil everywhere. Needless to say the transport and safety people were not at all amused to say nothing of
Photo caption –
No. 4 Machine.
T.H. Combination rig, (ex Canada)
Ready for action, Mar. 1999.
Page 20
severe damage to our perfectly good module which to this day still awaits reinstating. However, matters were resolved between parties including claims. It’s Ironic that this should happen so close to home after travelling all those distances. There are many comments Doug could make but for purpose of this shall decline. As they say in aviation “accidents/crashes just don’t happen – THEY ARE CAUSED !”
Mar, 2001 Greg became enthused on a machine in Western Australia, although basically a good unit was somewhat quite shabby and run down. Drilling in W.A. was in a bit of ebb at that stage. A price was offered which wasn’t expected to be accepted. However, it was — (didn’t know whether this was good or bad?) and our company became “proud” owners of No.6 rig, a Schramm T660H with its large 900 CFM @ 350 PSI compressor. This was based in Kalgoorlie, it hadn’t been physically viewed, so a bit of a “pig-in-a-poke”, however the price had to be right, so unseen was transported to Fremantle, then shipped all the way to Napier. Arrived OK & wasn’t far below expectations, basic unit was all there with potential good value. Over the next 16 month period much refurbishment, cleaning and repainting was carried out and with unit placed on a nice 4 axle Mitzi, emerged looking very smart and at last, excellent heavy rig ready for work July 2002.
This No 6 Scchramm machine along with most others, has also kept busy on some of larger projects, local councils, C.H.B. irrigation wells, etc, with its added tooling and improvements.
Sept-Oct, 2001 This signalled some very major changes to the drilling industry in H.B. and beyond, due to local rival Company needing to wind up its operations. This in turn brought our own Company having to make serious decisions and planning in a short space of time;also required Murray’s involvement. The business concerned planned to cease trading on 20th November, 2001. Plant and equipment was sold a month later with our company subsequently taking over most of this in early 2002, meaning considerable unexpected outlay, much of which we could have done without at the time; however, with cash flow, funds from other sources and my loan, costs were within manageable limits and more-so as trading and turnover increased into 2002. Much of the additional equipment put to good use with some sold off over time without haste at good market value. Due to this, Victoria Street workshop yards became overloaded and crowded at times compounded by un-necessary gross untidiness.
Mid 2002 Resulting from this additional plant, company now had 8 rigs, (not all operational), 3 crane trucks, 1 very large mobile compressor + a number of service trucks and utes plus assorted trailers with long list of ancillary gear in addition to large stock of casing, rods, etc. So Greg commenced searching for larger premises which in due course after looking at
Photo caption –
Jul. 2002
Schram 660 rig, ready for the road after many months of restoration including nice replacement Mitsi. mount (Unit No. 6)
Page 21
various alternatives, was most fortunate to locate a large ex pack-house with over 3 acres of land on western highway (Omahu Road) well sited on Hastings main industrial strip. The property has excellent amenities, large areas of thick concrete, well drained, plus ½ acre (2020 sq.M) of buildings including cool store and offices etc. Greg set about to negotiate and arrange purchase of property for a Trust he formed with himself and wife Catherine to in turn lease premises to the company and other future tenants. Deal was finalised around September, 2002 and the big move commenced from 406 & 408 Victoria Street which took all of October to complete after 33 continuous years there.
Many improvements proceeded at 1255 Omahu Road through to the end of year and into 2003, large doors, skylights, staff amenities, closing in southern end, grounds improvements to mention just a few. An excellent venue and facility for operating an expanding drilling and engineering enterprises: with property values in the proximity appreciating by the month.
June 2003 This replacement large “Western Star” 4 axle (8×6) tidy mount was purchased to conform to requirements of No.4 TH60 purchased 5 years ago.
So with this in view and requiring long down time period, Greg set about looking for another
Photo captions –
Interior of spacious new Omahu Rd. workshop
Dec. 2002
8X6 UNIT AQUIRED JUNE 2003
“WESTERN STAR”, UNDER PREPARATION & COMISSIONING AS MOUNT TO RECEIVE TRANSFER OF NO.4 RIG. (T.H.60)
Page 22
rig. After research another Ingersol-Rand TH60 was obtained in Milwaukie in July, shipped again from eastern seaboard and arrived Auckland September, 2003 with casing hammer but no other tooling. This No.9 rig is very similar to the No.4 TH60 but needed moderate amount of maintenance, bearings, clutches etc. otherwise reasonably tidy and with good potential after some more T.L.C.; — a good buy with pending work.
Would now like Greg to fill in some gaps here as my 50 year anniversary was to May, 2003. So will ask Greg to continue this narration one day & in due course, continue the ongoing story of our business & its small contribution & dedication to this huge vital staff of life —— WATER!
FOOTNOTE; Doug’s Personal Narration & Comments
Photo captions –
HONNOR WELL DRILLERS LTD.
No.9, INGERSOL-RAND, T.H.60, OCT 2003
Volvo with Greg & Steve at wild Ruatoria adventure, summer 1990
Page 23
I have no regrets in commencing as a one man plumbing business using own capital I had worked & saved hard for, albeit not a lot. Had minimal other assistance. In hindsight, the most valuable being examples & principles set by my good folks in my formative years (fortunately, at least some of it must have sunk in) It has been stated by some of the current generation that ours had the best of good economic times. While this may be true to some extent, (just too young to be called into war service) — they are naive & oblivious in many respects as most of our childhood years were during the great depression; while there were plenty of goods, there was no money to buy them. Like most others, our folks were extremely hard-up, therefore us kids had to make do, i.e. sell bottles to get 6d. (5c) for the movies–or go without. There were very few cars on the roads, most adults had bikes, others just walked or some able to catch a bus if lucky.
Then came the war and with it rapid changes–full employment, money available, but drastic shortage of goods followed, rationing, inflation with associated deprivations for the war effort; so those on the “home-front” were materially not much better off than in the ‘30s. In hindsight, these hardships were a good learning curve & taught us how to save & do not waste, so please don’t tell us we had it that easy,–& latterly having to put up with the last 30 years of Rock music!! Yes, there were some good years during this period, but you needed to make the best of them–& history shows many just still didn’t!
Another factor was commencing my apprenticeship in 1944 @ 16s.6d ($1.65) per week! To further make this relative, it equated to one-tenth of the journeyman’s wage for the privilege of learning this craft.
Rode the push-bike 2.5 miles (4k.) to work until almost 21. Good disciplinary training to make one really appreciate values which if correctly applied in due course paid off (although sure didn’t think so at the time as some of my contemporaries were earning five times as much at the Freezing Works) .—-Don’t know how some of today’s youth would handle this type of trade training ? Probably OK if made to, but in some respects, sad they are being deprived of much needed discipline thanks to our “permissive society”–Enough said.
Certainly there were better and more lucrative occupations at the time of commencing business in 1953 & onwards (a land agent or speculator perhaps); however, I found plumbing with its wide variation of skills an interesting active occupation which kept one fit and alert. Also was in the productive service and creative field which in that respect is more useful & gratifying.
What would I have done different? Like Bob Jones, I would have used other people’s money which was ridiculously cheap at the time, borrowed much in the 1970s and into the early 1980s and bought more properties and other tangible rapidly appreciating assets with other people’s money; however, it is always very easy to be wise in hindsight and we are not all as clever as Bob Jones in this field. Anyway, couldn’t complain about my small 1970s property investments. We all know what happened to those with shares in the late 1980s (myself, one slightly) so timing was & still is the essence plus a very good crystal ball. I could have taken more risks and been far more successful — perhaps?
Also worth mention that over all those years was never out of a job. Always busy, even during economic downturns and long wet spells, much due to diversification. There were odd slack periods, but this was offset by catching up with much workshop and equipment maintenance, preparing materials and sheet metal manufacturing (ridging, B-roll, tanks etc) in the plumbing days.
Page 24
Business stock Found this to be a good more reliable hands-on investment where one was in control & buying in their own field of knowledge providing quantity purchases were ordered for better discounts and paid for prompt. A shrewd buyer built up a good honest rapport and never messed the merchants around (returning goods etc) which added considerably to profitability of both plumbing and well drilling enterprises.
Plant & equipment: – Prior to mid 80s, there was minimal demand for larger & deeper wells throughout the district. Up to then our existing gear was more than adequate for current requirements by being kept well maintained & improvements to tooling. Cost-benefit up to that time would not have shown any significant advantage to justify further outlay; there was just not sufficient need with Co. showing good % return on turnover in spite of vicious environment we had to endure. But by management not being extravagant, it transpired we were far better placed than our larger rivals which in time proved only too true. Being, at one stage, having to exist with four drilling businesses here: plus the odd cowboy fly-by-nighter. (Jack Oates etc.) Bluntly, there was just not enough room for such. Fortunately, diversification within the business helped considerably. Emphasis was to invest & maintain significant levels of stock. This always paid off; indeed there were odd occasions where merchants borrowed/purchased material from us!
Incredible the changes that have taken place in more recent years, some including: —
- Demise of a major rival Co., (John Hill) Nov.2001, mainly due to their suicidal price cutting: (ultimately to our benefit)
- The huge amount the rural community being now prepared to invest such numbers in these large high capacity deeper wells:
- Being fortunate to have experience & service of Murray Gillies (ex J. Hill) to help meet these demands.
- Expansion of associated pumping & irrigation systems, hitherto absolutely unheard of.
- Entry into pre-collaring, starter holes locally for the oil exploration, (then subsequent geothermal further afield).
This in turn is of great benefit to the district, our Company profits — & the Nation, resulting in significant increases in primary production. Our Company/Greg has risen to take advantage & meet the demand of these changing times with their ongoing complexities. Although at times capital outlay is frightening, — Company remains comfortably very solvent as the 50th year closed with a firm & solid outlook into the future.
Oct. 2003.
End.
Page 25
Photo captions –
Glider releasing water ballast.
(Water has so many unknown important uses !)
L. Leader’s site, Ohiti – Matapiro area.
In process of suppressing & grouting off 6″ exploration well to control 30 psi. which relates ro [to] massive 70 Ft. head.
15 11 2005
On Greenies, pollution & environmentalists, 2009
I deplore filth, waste, untidiness & resent un-necessary desecration. So in a sense, I am a common-sense conservationist.
However, I cannot close this off without final say relating to double standards of these dreamers, some of which are scruffy dope smoking selfish stirrers (Nandor & Co.), others just resent other’s success, thereby impeding progress with costly delays & distress to wider NZ tax paying community. It was fortunate these types weren’t around when the country was being pioneered.
I refer to some instances relating to wind turbines, hydro works, mining etc. With all our Govt restrictions & requirements, today’s mining Cos. leave environment in better shape than
Page 26
when started & in the meantime generate much wealth & employment for the wider community. So in many instances, so called pollution is a myth. I grew up on an orchard & during the 1940s in my teens, was around to frequently help with spraying. Arsenate of lead was used extensively in effort to control the scourge of Codling moth. We shook these paper bags of fine powder into the mixing vat for spraying. Large multi nozzle high pressure “brooms” were used in those days, so operators also got a fair exposure to the mist spray. Sometimes the vat overflowed at filling point, so concentration of mix was deposited as well as throwing the empty bags onto a heap there & burning them ! resulting in toxic smoke-fumes of which we were oblivious. Then enter DDT: — this became generally used, the spray smelt like custard powder & a marvellous benefit for eradicating Codling moth, but now long since banned.
So with all the present day fuss about small remnants of lead & DDT residue, all the orchardists of that era, including myself certainly should have died many years ago.
Furthermore, us plumbers beat & handled large quantities of sheet lead, used much white lead paste, used lead paints, melted down lead in confined areas, Then in 1951-52, I worked on the lead-zinc mines at Broken Hill. So again, if you believe the Greenies, I definitely shouldn’t be here at age 80 in the year 2009. Major concern of paint on children’s toys & flaking weatherboards is overkill (pun). Our generation thrived on gnawing it. Where are the children & paint scrapers in the past that have been killed by this?
Much the same can be said about asbestos. Again, we used asbestos powdery pulp to lag boilers, mixed it up into water with bare hands. Used asbestos rope, cut asbestos-cement fibrolite sheets & pipes with associated dust; along with hundreds of other plumbers & builders through into the 60s & beyond. No doubt this is hazardous & lethal over period of concentrated exposure to its dust and some died. Obviously more so with some people than others. But now the over-reaction where it is located is just plain crazy. Are these costly un-necessary measures devised to keep our grandstanding Greenies, bureaucrats & odd-Bods in overpaid jobs?
Having said all above, stress that asbestos & lead under certain conditions can be & is highly lethal, particularly in prolonged exposure. In our plumbing tuition, obviously we were taught much about precautions, history & various forms of lead. For instance, house painters used much red & white lead (we also used some); some of these early day painters would mix & stir up the white-lead pigment with their bare hands. The most vulnerable area being quicks of finger nails for concentrations of lead to enter the system. Lead is a cumulative poison & unlike alcohol, is not expelled by the system or broken down, therefore such high concentrations become deadly and fatal for some.
History also tells us that lead was thought a contributing factor to the demise of the Roman Empire. The upper crust of society ate off & used many lead utensils, also water stored & supplied through lead pipes which could be detrimental if contained a low Ph. Was it this that helped send Nero & his cronies’ crackers?
Now coming forward, there is another device far more common & lethal in everyday life which everyone –including our Greenies happily use, — that being our motor car. Example: — just close yourself into a small garage with sweet engine ticking over for very short while & Bingo — all life extinguished! Now why don’t our Greenies along with traces of lead on Chinese toys, also ban motor cars? In spite of this, we still manage to survive.
Greenies & nutters, continued: —
Page 27
While on this subject, also cannot let it pass without stressing local water quality versus bottled water:–
There are so many parts of the world which have inadequate & contaminated water which I certainly would not consume and we buy bottled water when in places like Malaysia. In spite of this, millions still drink it & survive, (become immune) Millions more have also died, continue to die & suffer from festering water-born diseases & the squalor of multiplying over-population which is greatest pollutant of all, —- just too many people due to lack of birth control !
However, here in lucky NZ, by legislation, municipal supplies are up to & usually exceed world health standards. Under most parts of our Plains & Hastings-Napier in particular, we have amongst, if not the best quality water in the world. Supply comes straight out of aquifer via our artesian wells into the mains, no treatment required, has small additive to help children’s teeth. Yet we find it unbelievable these “Refrigerators to Eskimos” type people are buying bottled water here @ same price as petrol, when they can take a few paces to nearest city supply tap & get same or better water for nothing!
D.H.H., 2009.
(– and so I fade into the sunset….)
Page 28
Paul Bower’s pride, Farndon Rd., Sept. 1987.
— (And record free-flow of 84,000 GPH from 6” well still remains 2009).
Finally, —- Postscript, —some ongoing progress to 2006 + + —-
This following massive project among others bridged over a part of 3 financial years.
Bottom picture shows completed product with multitude of complex added features, which would now have to make it the top rig in NZ, in its size/class.
Page 29
A magnificent final achievement, August 2006.
(Photographic progress with narration of this complete project is shown in a separate file, “Western Star Story.
Photo captions –
Western Star progress, June ’05
August 2006.
Western Star TH-60, on first job, Ngatarawa after 20 months refurbishment.
Note air-hammer operation.
Non-commercial use

This work is licensed under a Attribution-NonCommercial 3.0 New Zealand (CC BY-NC 3.0 NZ).
Commercial Use
Please contact us for information about using this material commercially.Can you help?
The Hawke's Bay Knowledge Bank relies on donations to make this material available. Please consider making a donation towards preserving our local history.
Visit our donations page for more information.
Subjects
Business / Organisation
Honnor Well Drillers LtdFormat of the original
Computer documentDate published
2003Creator / Author
- Doug Honnor
People
- Dave Andrews
- Doug Ashby
- Vic Boag
- Paul Bower
- George Duley
- Rob Edgar
- Malcolm Gilchrist
- Murray Gillies
- Colin Gordon
- Doris Honnor
- Doug Honnor
- Greg Honnor
- Greg Horton
- Rex Ingram
- Herb Jillings
- L Leader
- Brian Liley
- Les Liley
- Ena McNabb
- Ray McNabb
- Jack Oates
- P Paton
- Eric Smith
- George Willan
- Tom Willan
Do you know something about this record?
Please note we cannot verify the accuracy of any information posted by the community.